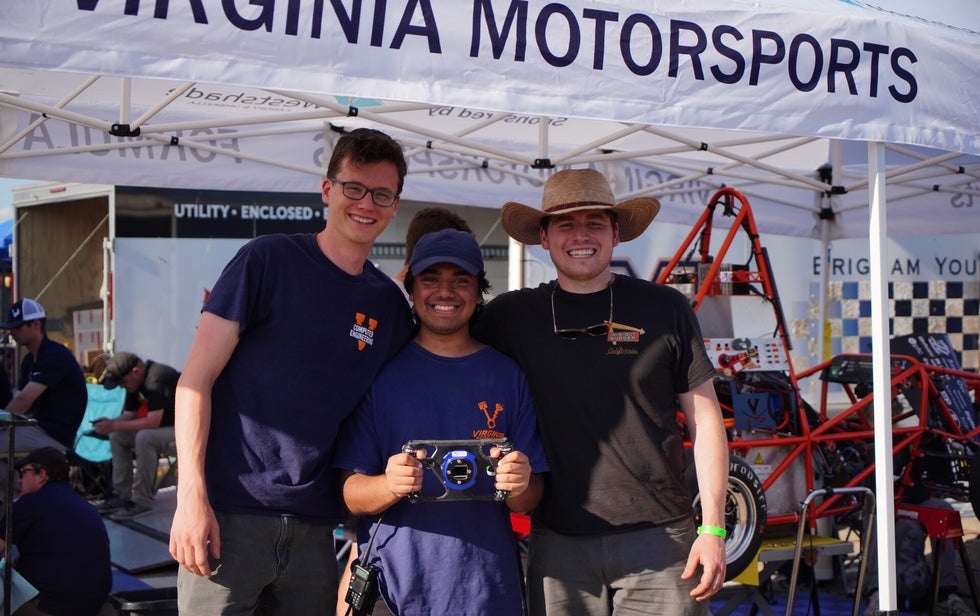
Cockpit/Controls
Pedalbox
For the 2023-2024 season, I was responsible for designing the pedalbox for the cockpit/controls subteam. Since we were transitioning to an electric vehicle, the pedalbox required a complete redesign. Success criteria included a >25% reduction in both weight and footprint from the previous year, a brake pedal that could withstand a load of 2000N with a reasonable factor of safety per rules, an adjustment range to accommodate 5th percentile females to 95th percentile males, and a redundant accelerator pedal position sensor (APPS) for fault-tolerance.
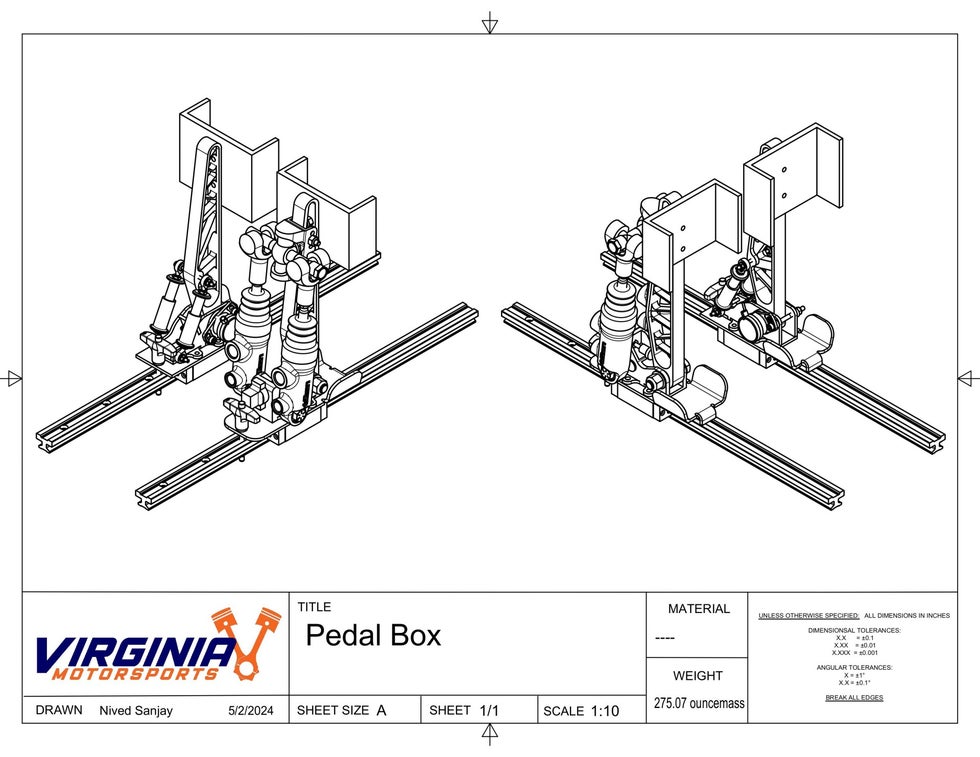
A single Variohm EURO-XPD rotary potentiometer was chosen for the APPS since it contains two discrete position sensors in one housing. I machined the entire assembly in-house from Al 7075-T6, incorporating webbed pedal bodies with flanged bent sheet metal faces covered in grip tape. The rear stop and return spring pre-load is adjustable on the accelerator pedals, and an adjustable brake ratio component was integrated via the Tilton 72-280 balance bar which was connected to a knob in the cockpit for on-the-fly adjustment. The difference between the minimum and maximum settings was ~5lbf to lock all wheels, accomodating drivers of different strengths and foot sizes. Heel rests were built into the base plates, and the pedals were discretely adjustable over a range of 18 inches using quick release ball-pin locks and Igus DryLin linear rails.
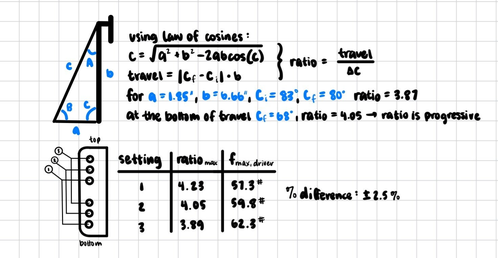

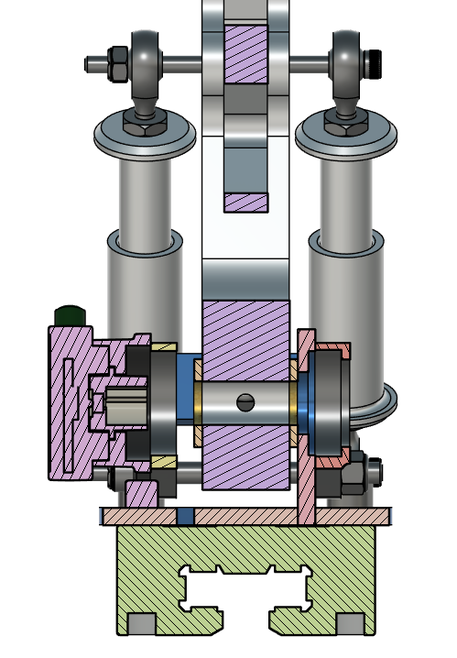
Steering Wheel
I was also tasked with designing a quick-release steering wheel for the 2024 car. The previous design used aluminum sheet metal sandwiched between sheets of carbon fiber, so there was room for significant weight reduction. Without the need for paddle shifting, there was more ergonomic freedom since the wheel could be gripped fully at all times. The wheel was made from a carbon fiber/kevlar weave sandwiching a piece of foam, and the edges were sealed with structural epoxy. Billet aluminum potted inserts were epoxied into the foam so that the quick connect could be attached. 3D-printed prototypes were used to gauge driver preference, and feedback was incorporated heavily into the final design.
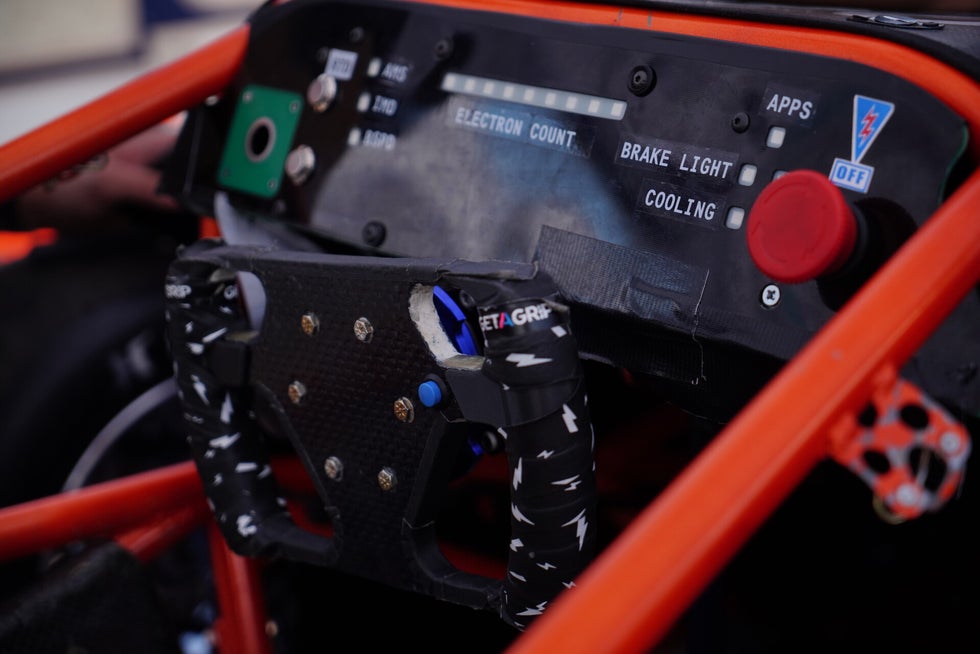
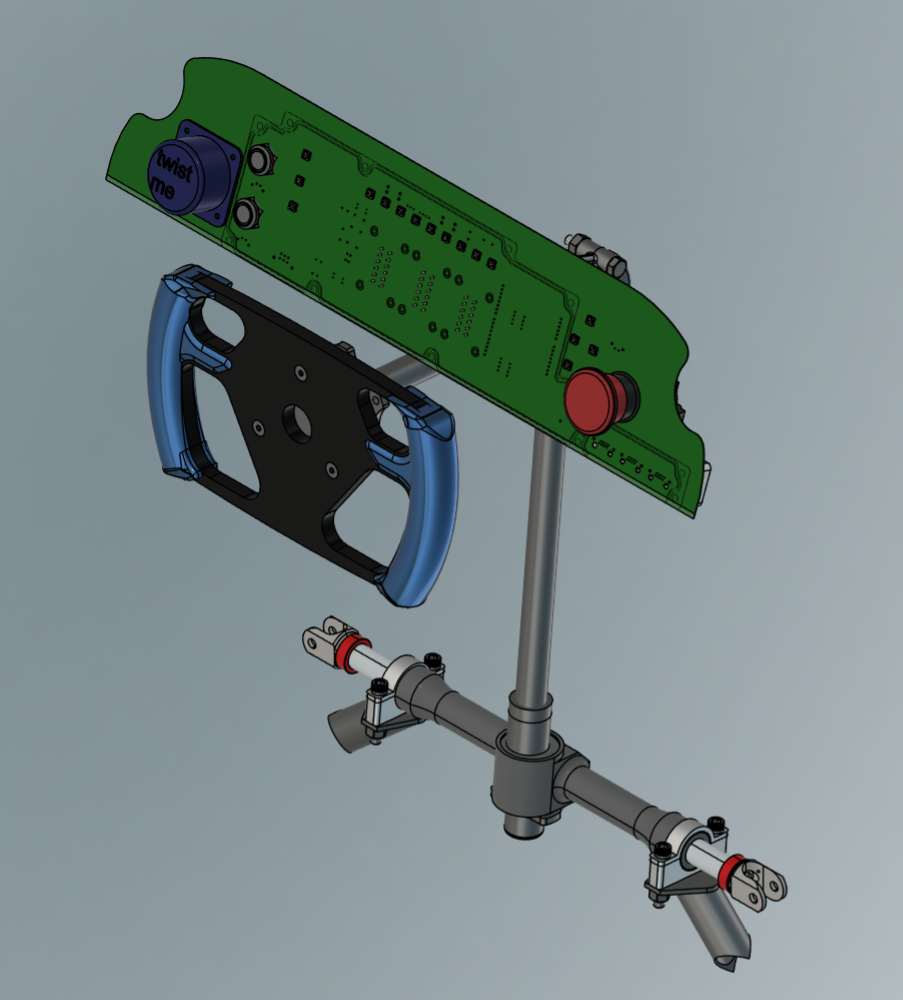
Suspension
Bell Cranks
I designed and manufactured the suspension bell cranks for the 2024 car. The bell cranks were designed using a static loading analysis of the suspension I did in Python using physical vehicle parameters, taking into acount six different load cases. The bell cranks were constrained by a motion ratio of 0.8 and maintaining as linear of a motion ratio as possible through 2" of wheel travel, taking care not to allow the suspension to invert at full compression. Weight savings was a primary goal for the front rockers, achieving over 50% lighter assembly than the previous year. For the rear rockers, packaging was heavily constrained by the push-rod layout and clearance to rear chassis tubes, but a motion ratio with a linear correlation of 0.99 through all 2" of travel was achieved. All rockers include integrated conical bosses to keep rod end bearings captive as well as welded bolts for linear potentiometers that measure spring travel, and the fronts include anti-roll bar mounting points. I machined the bell cranks in-house from Al 7075-T6.
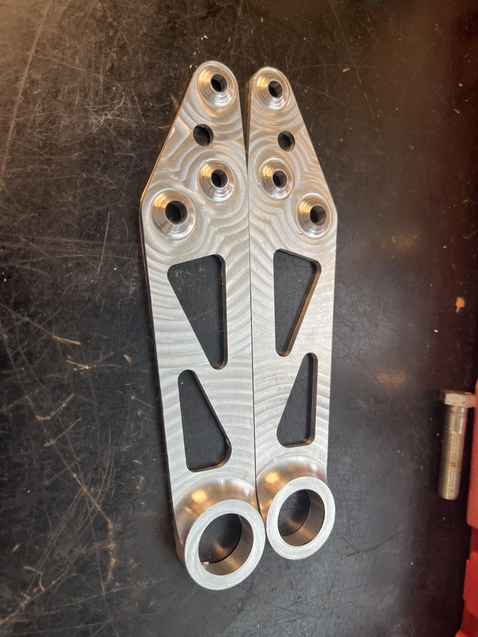
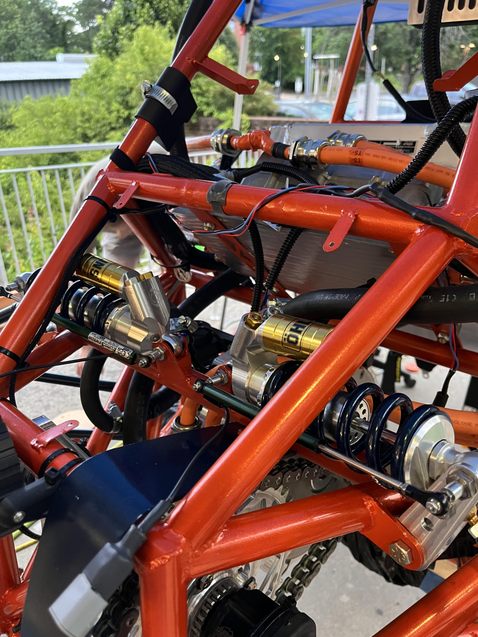
Anti-Roll Bar
I designed and manufactured an anti-roll bar to facilitate suspension adjustability and testing. Pillow blocks constrained by shaft collars with flanged oil-impregnated bushings were used to allow the ARB to rotate freely and keep loads in plane (no lateral shifting of the bar). Calculation of the ARB rate involved computing the torsional stiffness of the bar and translating this to a linear rate at the wheel, taking into account the installation ratio from the bell crank to the wheel. The ARB was constructed from welded 4130 steel, and the pillow blocks were made from machined aluminum. Research and development was also done for a bladed cantilever anti-roll bar for the 2025 season.
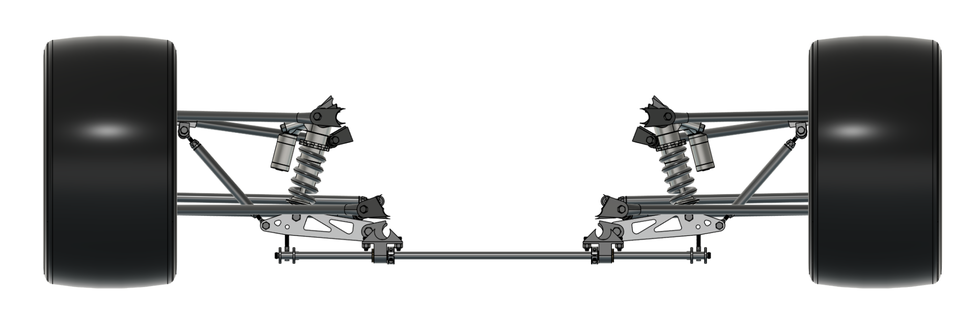
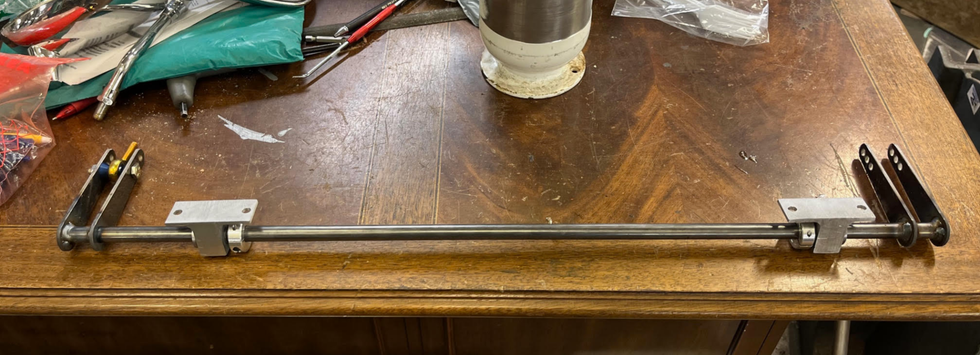
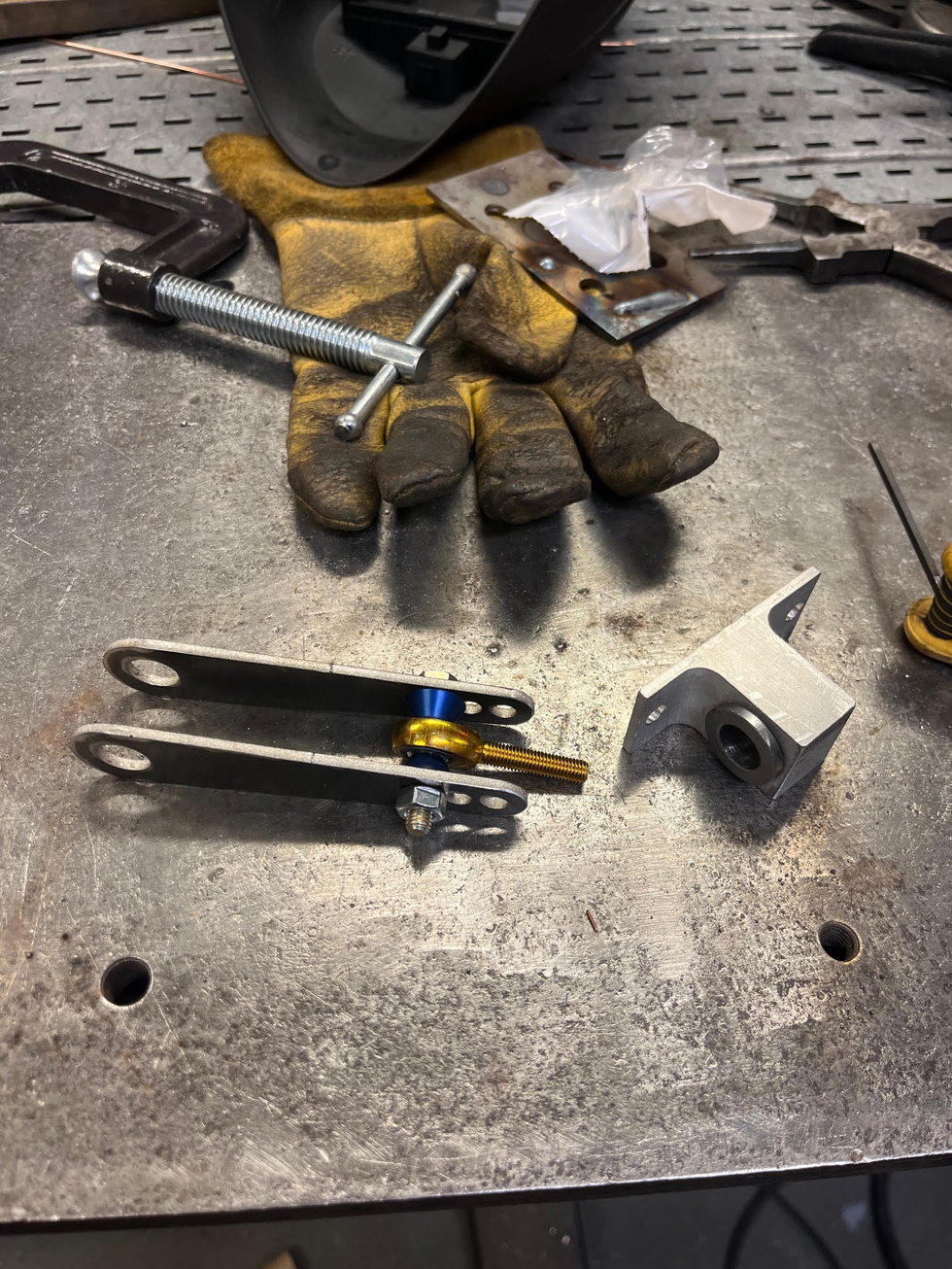